摘 要:介紹了活性石灰回轉窯生產系統(tǒng)用耐火材料應用現狀、功能耐火材料新產品研發(fā)及應用。通過功能型新材料研發(fā)和整體結構設計,優(yōu)化該系統(tǒng)耐火材料內襯配置,解決活性石灰系統(tǒng)關鍵部位和易損部位耐火材料現有問題,使之各個部位耐火材料內襯使用壽命基本同步,減少停窯檢修次數,有效延長窯爐使用壽命,提高生產作業(yè)率,降低能源消耗,提高資源綜合效率。
活性石灰回轉窯主要應用于鋼鐵、鐵合金、氧化鋁及電石行業(yè)用活性石灰和輕燒白云石?;钚允一剞D窯煅燒系統(tǒng)主要設備包括預熱器、轉運溜槽、回轉窯、燃燒裝置、冷卻器等設備,整套系統(tǒng)設備操作可靠,自動化程度和勞動生產率高,產品質量好。
活性石灰生產線耐火材料使用過程中存在著高溫段侵蝕嚴重,容易發(fā)生掉磚,塌窯等現象,回轉窯高溫段、窯口、轉運溜槽等關鍵部位內襯使用壽命短、壽命不均衡、作業(yè)率低及能耗高,制約了該設備優(yōu)勢的發(fā)揮,嚴重影響活性石灰的質量和產量。根據活性石灰回轉窯耐火材料損壞機理,從新材料研發(fā)、砌筑結構優(yōu)化、節(jié)能降耗等方面對耐火材料進行集成優(yōu)化設計和全面研究,突破行業(yè)界限、關鍵技術,先后研發(fā)了系列配套功能耐火材料及整體解決方案,該整體解決方案長壽、高效、穩(wěn)定、安全運行,節(jié)能降耗。
1 耐火材料應用現狀
回轉窯、預熱器和冷卻器耐火材料內襯對設備運行起著關鍵作用,耐火材料的損壞直接影響整個生產線的正常運行和設備壽命。目前,活性石灰回轉窯耐火材料應用主要存在高溫段侵蝕嚴重的問題,容易發(fā)生掉磚、塌窯,且窯口、分倉隔墻、轉運溜槽等關鍵部位內襯使用壽命短,壽命不均衡。
1.1 回轉窯用耐火材料
傳統(tǒng)石灰回轉窯砌筑常采用鎂鋁質燒成磚或不燒磚砌筑結構,該材料及砌筑結構導熱系數高,回轉窯筒體外表溫度在300℃以上,能耗極高。該砌筑結構不穩(wěn)定,常出現抽簽、剝落、掉磚甚至坍塌現象,具有極大的安全隱患。國內不少石灰生產線投產不到3個月即發(fā)生塌窯事故?;剞D窯窯口部位冷熱交替頻繁,物料持續(xù)撞擊與沖刷,使該部位耐火材料經常出現剝落現象,進而破壞鋼構件,需要經常進行停窯檢修。
1.2 轉運溜槽用耐火材料
傳統(tǒng)轉運溜槽及下料漏斗部位采用低水泥澆注料整體澆注或小磚砌筑結構,難以達到烘烤條件,強度低、耐磨性差。該部位物料持續(xù)撞擊與沖刷,使該部位耐火材料經常出現剝落現象。
1.3 預熱器用耐火材料
大部分預熱器料倉、分倉隔墻采用澆注料現場澆注施工,預熱器內部結構較為復雜,空間狹小,現場支模施工困難,澆注料流動不到位,容易造成的空洞現象。因此,施工時常通過增加加水量來提高澆注料的流動性,但是加水量的增加會大大降低材料的耐磨性,直接影響到澆注料的使用性能,造成該部位耐火材料的使用壽命較短,滿足不了使用要求,影響生產率。
2 生產工藝對耐火材料的影響
活性石灰回轉窯生產工藝操作的穩(wěn)定性、科學性是保證耐火材料使用壽命的重要因素,火焰燃燒、煤粉質量及燒嘴、轉子稱等設備因素均會產生重大影響,甚至能成為耐火材料損壞的直接因素。
2.1 火焰燃燒
回轉窯活性石灰煅燒工藝需要的熱量大部分是通過火焰輻射進行傳遞,火焰的溫度和形狀極為重要,火焰燃燒形狀對耐火材料使用壽命有重大影響。正常的火焰形態(tài)應該在窯內呈柳葉形,均勻對物料進行煅燒。如果燃燒呈現團狀,直接在耐火材料表面燃燒,會形成局部溫度過高,造成回轉窯耐火內襯局部坑狀熔蝕(見圖1)。
2.2 煤粉質量
煤粉粒度較大,未能在規(guī)定的部位充分燃燒,未充分燃燒的煤核在重力和燒嘴旋風的作用下落至耐火材料表面繼續(xù)燃燒,造成材料局部高溫,高溫狀態(tài)下煤核中的雜質低融物與材料發(fā)生反應,進而損壞耐火材料。
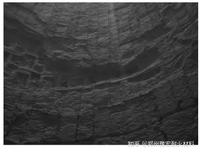
圖1 局部坑狀熔蝕形貌圖
煤粉水分大,水分是燃燒過程中的有害物質之一,它在燃燒過程中吸收大量的熱量,造成燃燒波動大,產生大量氣體,回轉窯內壓力波動大,是產生正壓原因之一,影響回轉窯內部溫度分布及穩(wěn)定性,造成耐火材料剝落或者熔蝕。
揮發(fā)分對燃燒的影響,揮發(fā)分小,火焰燃燒速度慢,火焰長度就會變長,高溫段就會向后移動,揮發(fā)分大,燃燒速度快,高溫段就會集中在回轉窯前段,造成耐火材料熔蝕。
長時間煤粉粒度、水分、揮發(fā)分等質量波動,煤粉爆燃產生局部高溫,在回轉窯高溫段造成坑狀連續(xù)熔蝕(見圖2)。
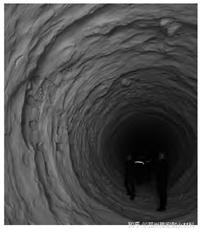
圖2 坑狀連續(xù)熔蝕形貌圖
2.3 頻繁停窯
頻繁停窯和快速升降溫使窯內耐火材料承受較大的剪切應力,導致材料內部產生裂紋,對材料造成隱性傷害,疊加回轉窯旋轉產生的周期性應力,在頻繁的內部應力作用下,材料強度逐步衰減。窯體在運行時成橢圓形,窯體轉動時耐火材料制品與窯體鋼構之間、耐火材料制品之間產生應力,當材料本身強度受熱震破壞后不足以抵抗應力時,便會產生材料成塊剝落的現象。
2.4 設備因素
(1)燒嘴
由于火焰長度較長,如燒嘴位置發(fā)生稍許偏移就會使火焰末端產生較大偏移,有可能造成火焰直接噴向窯體材料的情況,導致局部耐火材料持續(xù)受到火焰的烘烤,造成局部溫度過高,產生回轉窯耐火內襯環(huán)狀熔蝕(見圖3)。燒嘴長時間沒有維護或者結構不合理,燃燒不穩(wěn)定,造成溫度波動窯內壓力波動,影響耐火材料的使用壽命。
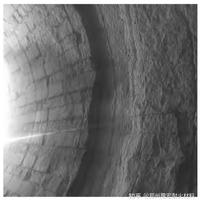
圖3 耐火內襯環(huán)狀熔蝕形貌圖
(2)轉子秤
轉子秤計量不準確,造成煤粉單位時間供應量波動比較大,從而影響燃燒的穩(wěn)定性,造成溫度波動窯內壓力波動,影響耐火材料的使用壽命。
3 功能耐火材料的研發(fā)與應用
根據耐火材料損壞機理及活性石灰生產工藝狀況,通過研發(fā)功能耐火材料,優(yōu)化耐火材料材料內襯配置,解決活性石灰系統(tǒng)關鍵部位和易損部位耐火材料現有問題,使之各個部位耐火材料內襯使用壽命基本同步,減少停窯檢修次數,有效延長窯爐使用壽命,提高窯爐生產作業(yè)率。
通過對用后耐火材料進行電鏡掃描分析,研究回轉窯高溫段有關耐火材料損壞情況及機理,根據不同損壞機理結合工況條件,先后研發(fā)鎂鋁尖晶石澆注料、鉻剛玉尖晶石復合澆注料、鋼纖維增強剛玉莫來石復合澆注料等使其具有耐高溫、抗堿侵蝕及物料沖刷功能,解決耐火材料侵蝕嚴重、內襯壽命短的問題。鎂鋁尖晶石澆注料及預制磚,具有抗剝落功能,解決普遍存在的回轉窯剝落影響生產順行問題。并對低硫石灰、低生燒石灰煅燒工藝及對耐火材料侵蝕機理進行研究,提高耐火材料對低硫石灰煅燒工藝的適應性,進一步延長低硫石灰、低生燒石灰回轉窯內襯使用壽命。
3.2 轉運溜槽、窯口等關鍵部位耐火材料
轉運溜槽、窯口部位耐火材料物料沖刷嚴重,通過研究損壞情況及機理,采用超微粉技術、凝聚結合技術、斷裂增韌技術、鋼纖維增強技術以及原位反應技術,充分發(fā)揮了莫來石相的耐急冷急熱性和剛玉相的高溫耐磨性,具有體積穩(wěn)定性好、熱震穩(wěn)定性強、耐侵蝕、耐沖刷、強度大等特點。開發(fā)的窯口專用料具有強度大、耐磨損、耐侵蝕等特點,使用壽命2年以上(見圖4)。
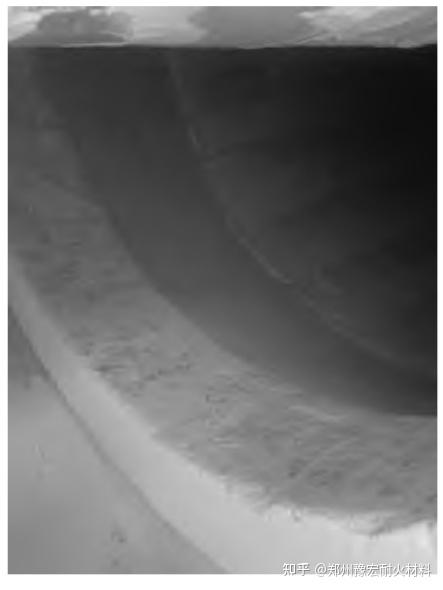
圖4 窯口部位耐火材料形貌圖
3.3 高耐磨耐火材料
采用耐磨性極好、熱震性良好的高純原料,通過合理搭配,利用流變學原理、最緊密堆積理論、凝聚復合技術、增韌技術和超細粉技術,主要研究結合劑的選擇與加入量對高強耐磨材料的性能及組織結構及耐磨性能的影響,特殊添加劑、顆粒級配對流動性能的影響,助燒劑的選擇及對耐火材料耐磨性能的影響,研究開發(fā)高耐磨澆注料,在預熱段上使用壽命延長2~3倍。
3.4 高強度噴涂料料及噴涂修復技術
關于高強度噴涂料及噴涂修復技術,針對活性石灰回轉窯的特點,通過材料選型及顆粒級配優(yōu)化,研制開發(fā)高強度噴涂料及噴涂修復技術(見圖5),對耐火材料內襯進行修復,延長耐火材料使用周期。在多家石灰生產系統(tǒng)回轉窯應用,可延長使用壽命2~4個月。
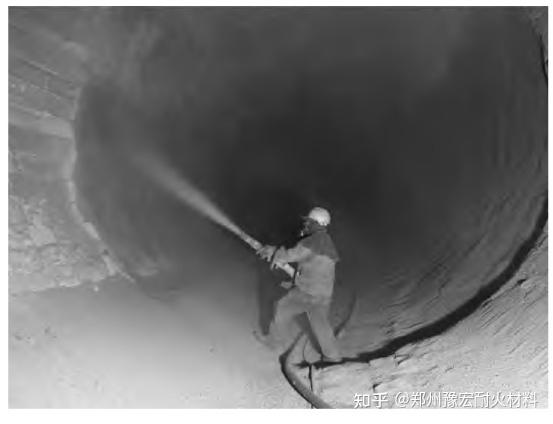
圖5 回轉窯內襯噴涂現場圖
3.5 快速烘烤防爆技術
優(yōu)化材料結合系統(tǒng),使材料具有可快速烘烤的特點,同時在使用過程中,各個溫度段均保持高強度,高耐磨性。該材料適合于短時間臨時檢修,比常規(guī)澆注料烘爐時間節(jié)約一半以上。
4 綜合砌筑結構優(yōu)化與改進
通過對活性石灰回轉窯生產線耐火材料內襯整體設計,對砌筑結構進行優(yōu)化與改進,大幅提高了易損部位的使用壽命,耐火材料內襯壽命均衡,提高了耐火材料內襯的整體使用壽命,提高設備作業(yè)率,降低設備能耗。
4.1 回轉窯
通過和客戶技術人員充分交流及實地考察,針對活性石灰工程耐火材料進行詳細分析,對新型耐火材料品種進行推廣應用,同時積極進行砌筑結構改進?;剞D窯窯襯砌筑采用預制磚和澆注料的綜合砌筑(圖6),根據回轉窯直徑及工況條件,沿圓周方向等分為若干等份,每一份砌筑預制磚和澆注料各一條,保溫層采用陶瓷纖維,整體解決方案長壽、節(jié)能、安全、高效。
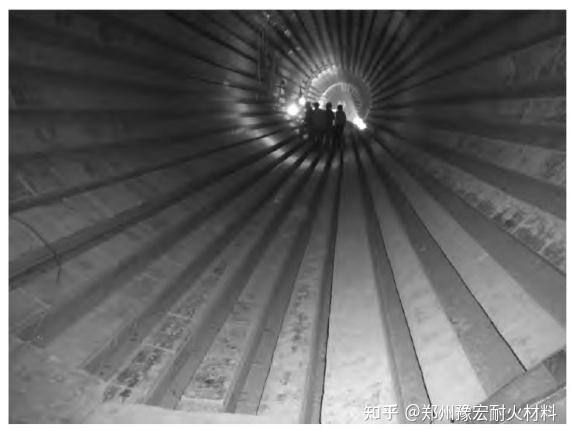
圖6 回轉窯綜合砌筑現場圖
(1)長壽:正常使用條件下,高溫段質量壽命2年以上,低溫段壽命3年以上。在中天鋼鐵1 000 t/d白灰回轉窯上使用3年后高溫段仍有220 mm,低溫段原磚厚度。 (2)節(jié)能:正常使用條件下,窯皮溫度在220℃以下,有效節(jié)約能源10%以上。 (3)安全:整體性好、不剝落、不坍塌。 (4)高效:20 d即可完成整條窯砌筑。 (5)生燒率低,石灰產量、質量高:該砌筑結構設置揚料磚,起到翻料、楊料和推料作用,促使石灰的充分、均勻干燥和預熱,降低了石灰的生燒率,提高了石灰的質量和產量。
4.2 推料平臺
推料平面采用隔熱磚、黏土磚、鉻剛玉耐磨磚分層綜合砌筑結構,隔熱磚緊貼爐體砌筑,然后砌筑一層黏土磚,最上層的工作層采用鉻剛玉耐磨磚,推料平面不能砌磚部位焊接錨固釘采用鉻剛玉耐磨澆注料澆注。使用該方法砌筑推料平臺的耐磨性好,維修更換方便、快捷。
4.3 下料漏斗
下料漏斗采用專利技術(一種豎式預熱器砌筑式下料漏斗及其豎式預熱器,專利號:CN202020755541.6),該技術方案采用下料漏斗預制磚、鉻剛玉耐磨磚混合砌筑的方式。預制磚焊接于設備上,可有效防止因振動和變形造成耐火材料脫落的發(fā)生,根據設備形狀特征,設計組合預制磚,能夠有效釋放熱應力和機械應力,預制本身經過預制成型、烘烤,耐磨損、耐沖刷、耐侵蝕,使用壽命有較大提高。
4.4 轉運溜槽體
溜槽體采用磚料混砌的結構形式,溜槽體斜平面、兩側斜面用溜槽預制磚焊接砌筑在鋼板上。溜槽預制磚之間的空隙采用鉻剛玉耐磨磚填充。溜槽體上不能焊磚也不能填充鉻剛玉耐磨磚的部位及舌頭部位焊接錨固釘,然后澆注鉻剛玉耐磨澆注料。
推料平臺、下料圓錐、轉運溜槽新型砌筑結構、燒嘴保護技術等解決該部位壽命短的技術難題,壽命提高到24個月以上。
5 節(jié)能降耗
采用輕質和重質耐火材料復合砌筑結構,預制磚及澆注帶設有隔熱性能優(yōu)異的陶瓷纖維材料做為保溫層,且窯襯材料內的沒有縫隙,杜絕了窯內熱量向筒體的對流和輻射傳熱,有效地降低了窯皮溫度,節(jié)約能源。通過研發(fā)導熱系數低的功能耐火材料新產品,進一步有效的降低設備外壁溫度,節(jié)約了能源的消耗;另一方面,通過長壽化、均衡化設計及新材料開發(fā)減少停窯次數,節(jié)約了每次停窯浪費的能源,節(jié)能降耗。窯體外部溫度有明顯降低,節(jié)能效果明顯,節(jié)能效果達10%以上。
6 結語
針對活性石灰回轉窯生產工藝條件,采用功能耐火材料新產品,通過功能耐火材料和綜合砌筑結構優(yōu)化,優(yōu)化耐火材料內襯配置,解決了活性石灰系統(tǒng)關鍵部位和易損部位耐火材料現有問題,使之各個部位耐火材料內襯使用壽命基本同步,減少停窯檢修次數,有效延長窯爐使用壽命,提高窯爐生產作業(yè)率,降低能源消耗,提高資源綜合效率。